
It also does excellent work with holes, a seemingly simple feature, but one that can get quite complex when entering the realms of multi-stage hole drilling or boring and threading (both of which have seen work in this release). The system will identify all the features it can, including Pockets, Bosses, Faces, Grooves, Chamfers and Sidewalls. This gives it more flexibility to adapt to machining requirements. To do this, FeatureCAM first identifies each feature (in terms of machining feature, rather than geometry) and does this using a proprietary algorithm (AFR, Automatic Feature Recognition), rather than reading the native features from the CAD package. The geometry is imported (or created from scratch), the global parameters set up, and then automation tools are used to set-up each operation. When working with a turning or mill-turn operation things differ somewhat as these parts are revolved, but the basics remain the same. That includes selecting the machine tool, the Z and X axes (so the system can orient it correctly), the origin and the stock material. As with all CAM operations, the starting point is to set-up the global parameters for the job. Whichever format is brought in, the workflow is the same. It also includes a range of native data import options, including AutoCAD, Inventor, SolidWorks, Catia (V4 and V5), Solid Edge, Unigraphics/NX, and Pro/Engineer.Īutomatic feature recognition looks for pockets, bosses, faces, grooves, chamfers and sidewalls – and uses best practice to apply operations to them FeatureCAM supports all of the major translation formats (such as IGES, STEP) as well as a number of native formats. To illustrate this, let’s step through a basic part programming job.įeatureCAM allows users to work with sketched geometry but a more intelligent way to work is to extract the required data from a CAD system. This enables it to make intelligent decisions and automate much of the workload, which it does by relying on feature recognition very heavily. By that, I mean that it does an excellent job of capturing knowledge and data about all those parameters, variables and inputs that influence part programming, such as cutters/tools, operations materials, and feature types. Whether carrying out basic 2.5-axis machining, 3-axis, 5-axis or into the realms of Mill/Turn, the key to FeatureCAM is that it is built on a very strong knowledge-based infrastructure.

In addition, where the system was perhaps best known for coding NC from scratch off the back of very basic 2D geometry (typically sketched by the user), it now has workflows for all manner of data sources and machining operations.įeatureCAM imports the majority of standard CAD data, and includes several native file importers
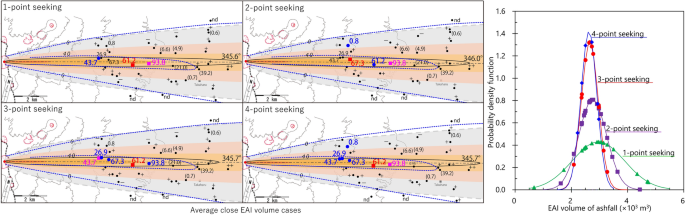
Support for 3D data has improved and the general look and feel of the system has been overhauled. It’s in this latter segment that Delcam’s FeatureCAM sits, and sits perfectly.ĭelcam acquired the product a couple of years ago, and since then a number of things have happened.
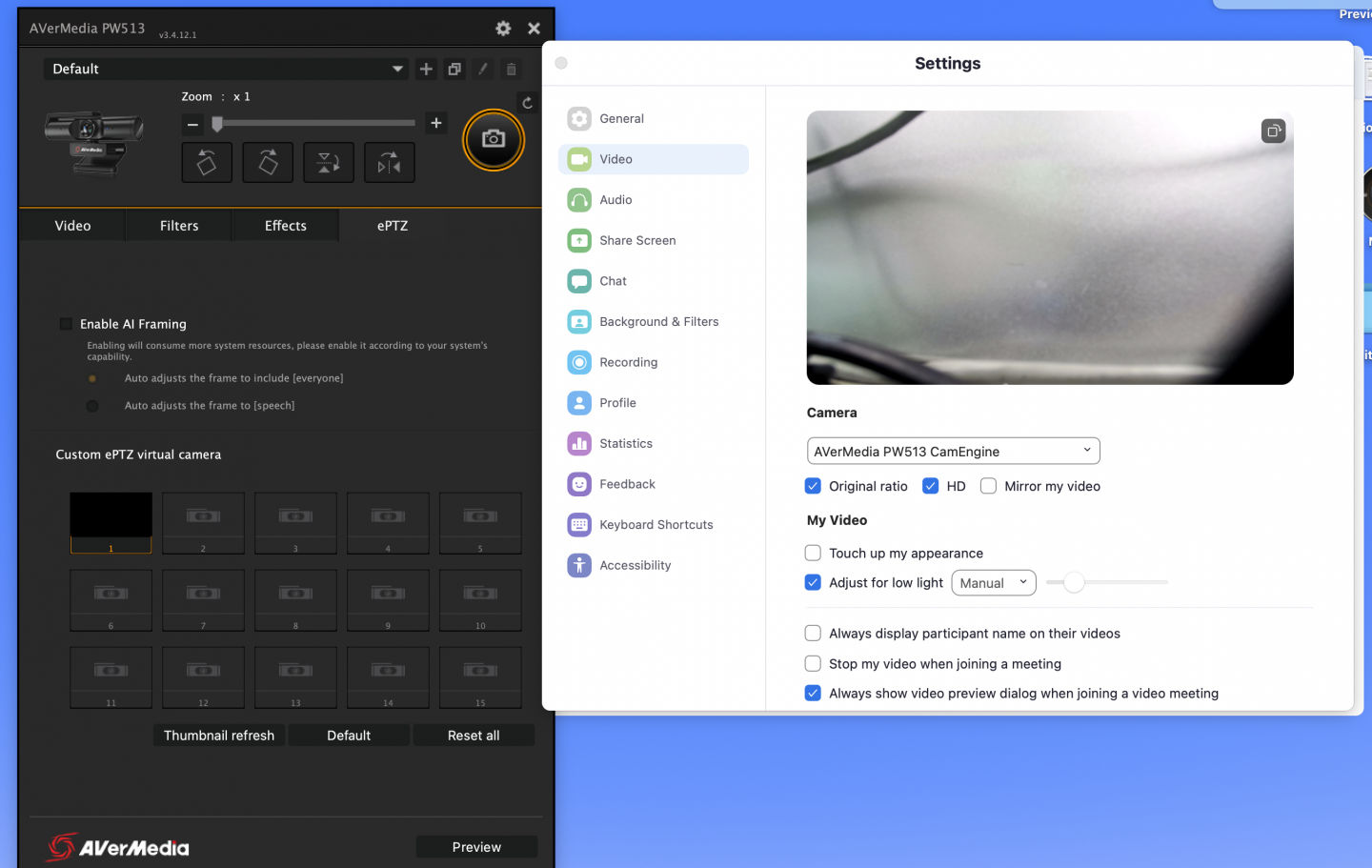
Some applications concentrate on the ability to machine complex geometry and control highly complex machines (such as within the Mould and Die market) while others focus on the world of production machining, where equally complex machine tools (such as increasingly popular Mill/Turn configuration) are used to produce less complex parts, but in typically much larger volumes.
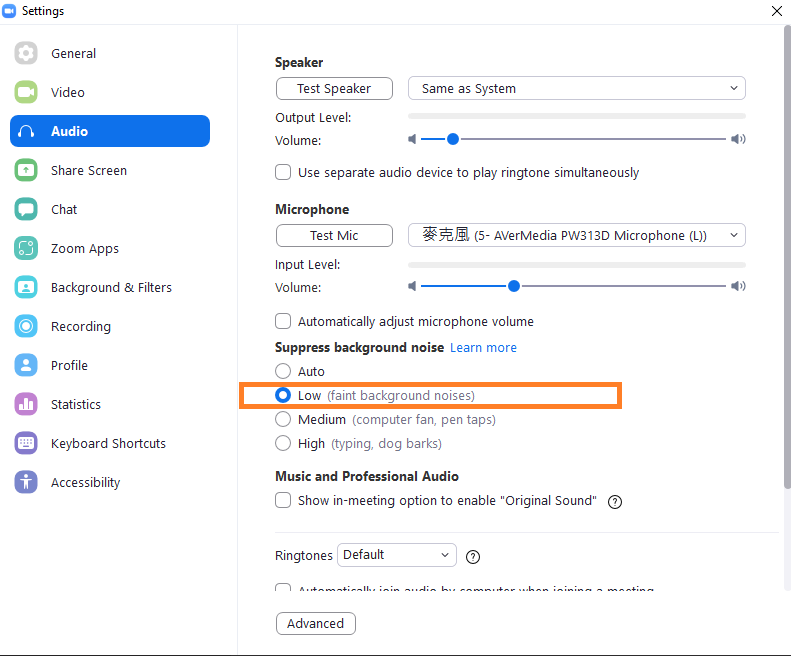
DelcamWhen you look at the world of Computer Aided Manufacture (CAM) and drill down (no pun intended) into who’s doing what and what the different systems offer, you quickly find something of a split.
